Noticias
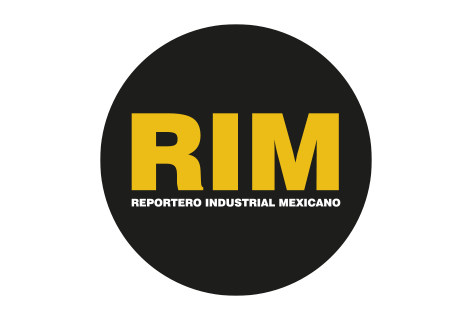
La sensorización industrial se está convirtiendo en aliado clave del mantenimiento al integrar datos en tiempo real y decisiones predictivas con impacto operativo y financiero.
El uso de sensores y sistemas conectados es cada vez más profundo en la manera en que las industrias entienden y ejecutan el mantenimiento.
Vea la entrevista completa
Esta transformación, impulsada por el internet de las cosas (IoT) y la digitalización, ha llevado a que las empresas transiten del mantenimiento correctivo al predictivo, donde las decisiones se basan en datos capturados en tiempo real desde los equipos.
Según Montzerrat Castañón, Technical Project Manager en Fracttal, “estamos en una época privilegiada para quienes trabajamos en la implementación de estas tecnologías, porque hay un cambio de mentalidad que permite que las empresas lo vean como el siguiente paso lógico”.
Uno de los pilares de esta transición tecnológica es la sensorización. Castañón señala que “la medición de vibraciones con sensores triaxiales se ha vuelto una práctica común en activos industriales como motores, bandas transportadoras o torres de destilación”.
Estas mediciones permiten detectar fallas antes de que ocurran, evitando paros no programados y daños mayores. Para ello, el hardware actual se ha vuelto más preciso, compacto y fácil de integrar. “La clave es contar con datos no sesgados y exactos, con alto valor y que no dependan tanto de la interpretación humana”.
En términos de conectividad, las empresas más avanzadas optan por arquitecturas específicas que consideran su infraestructura y políticas de ciberseguridad. Algunas adoptan redes cableadas tradicionales; otras, soluciones inalámbricas como LoRaWAN o Sigfox. A esto se suma la implementación de algoritmos de machine learning, capaces de identificar patrones, establecer umbrales dinámicos y detectar tendencias que anticipen fallos.
Impacto operacional
Los beneficios no solo se observan en confiabilidad operativa, sino también en el uso inteligente de la información. “El reto no es tener mucha información, sino tener información de valor que permita tomar decisiones concretas”, señaló la especialista en IT.
Esta capacidad analítica ha cambiado el comportamiento de las áreas de mantenimiento, producción y calidad, que ahora colaboran a partir de una base de datos común, lo que mejora las decisiones de compra, el seguimiento de activos y la planeación presupuestaria.
Un caso mencionado por Castañón ejemplifica el potencial de esta tecnología: un cliente decidió desmontar un equipo tras una alerta emitida por el sistema. Aunque representó un costo inmediato en tiempo y dinero, se evitó una falla catastrófica provocada por un rodamiento en mal estado. “La intervención oportuna evitó consecuencias mayores en toda la línea de producción”, subrayó.
Estos desarrollos están alterando incluso los esquemas financieros de las empresas, especialmente la depreciación de activos. “Hoy los sistemas de mantenimiento integran datos técnicos y financieros, lo que permite generar reportes analíticos que conectan departamentos que antes ni siquiera se hablaban”.
Esto permite a las organizaciones planear renovaciones de maquinaria con criterios más precisos, basados en ciclos de vida reales y no teóricos.
Para los próximos cinco años, se espera una mayor adopción de estas tecnologías en todos los niveles industriales. Ya no se trata de un lujo exclusivo para grandes corporativos, sino de una necesidad para mantener la competitividad.
La sensorización y el análisis de datos seguirán siendo claves para optimizar procesos, reducir costos y aumentar la eficiencia en la operación industrial.
Otros artículos de interés
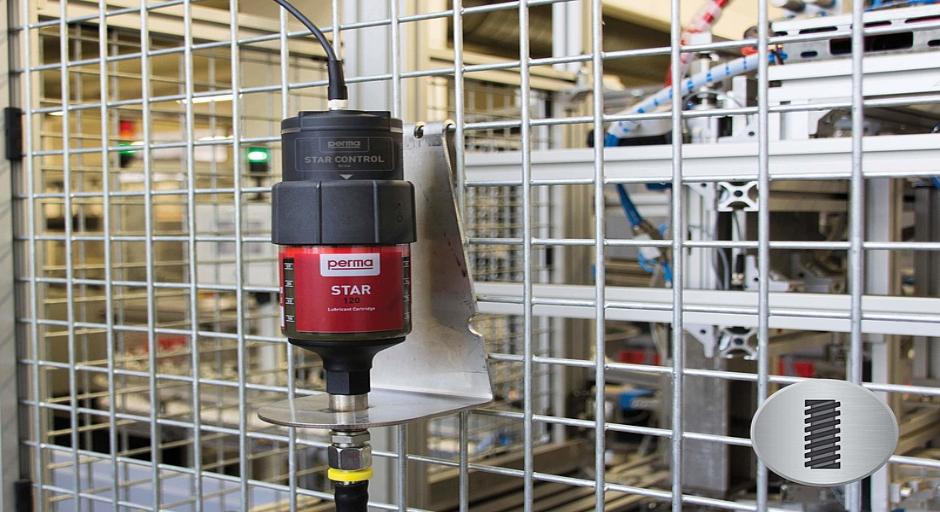
Lubricación automatizada, paso obligado en operación: Perma
En las plantas industriales, la lubricación ha pasado de ser una rutina
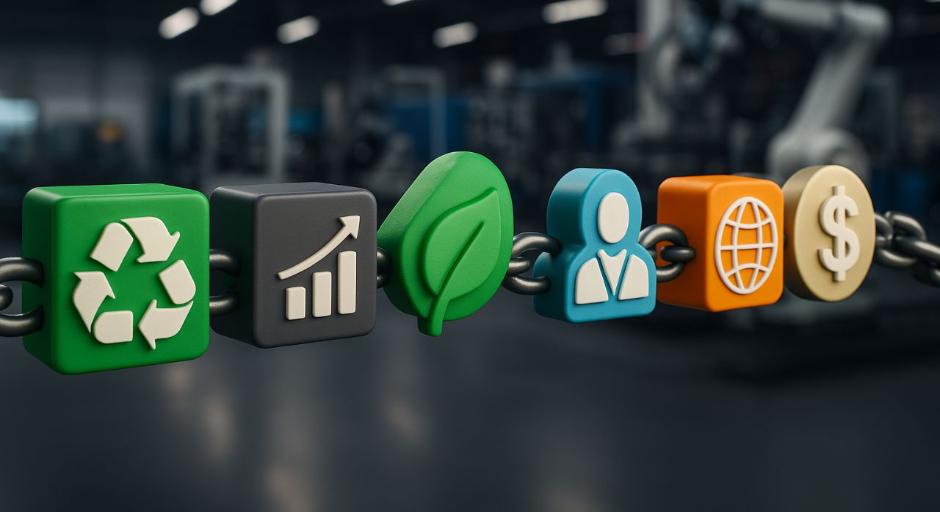
Cuidado ambiental: responsabilidad eslabonada
El cumplimiento de políticas de sostenibilidad en la industria manufacturera se ha
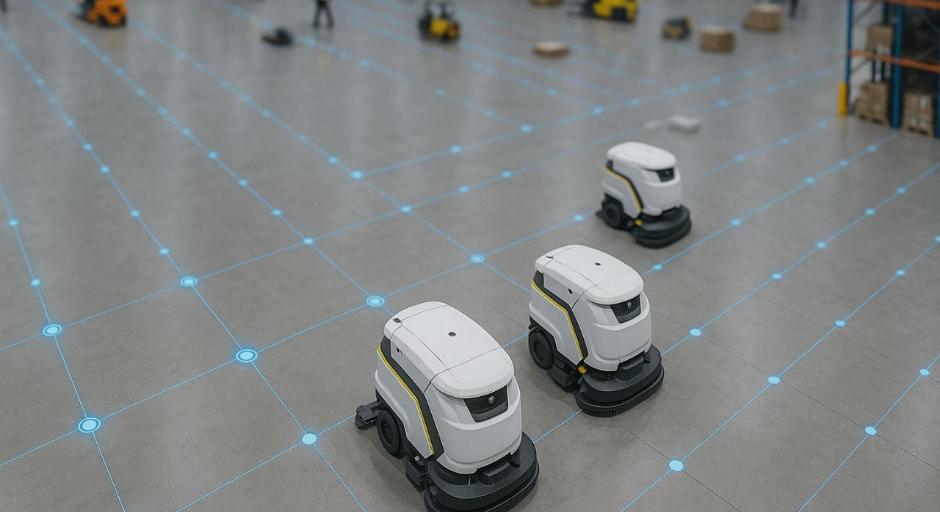
Limpieza industrial no escapa de la automatización
En la industria, la limpieza de áreas productivas es tan importante como

Suministro ininterrumpido para la Industria 4.0
La Industria 4.0 representa un salto evolutivo en la manufactura: sistemas físicos,
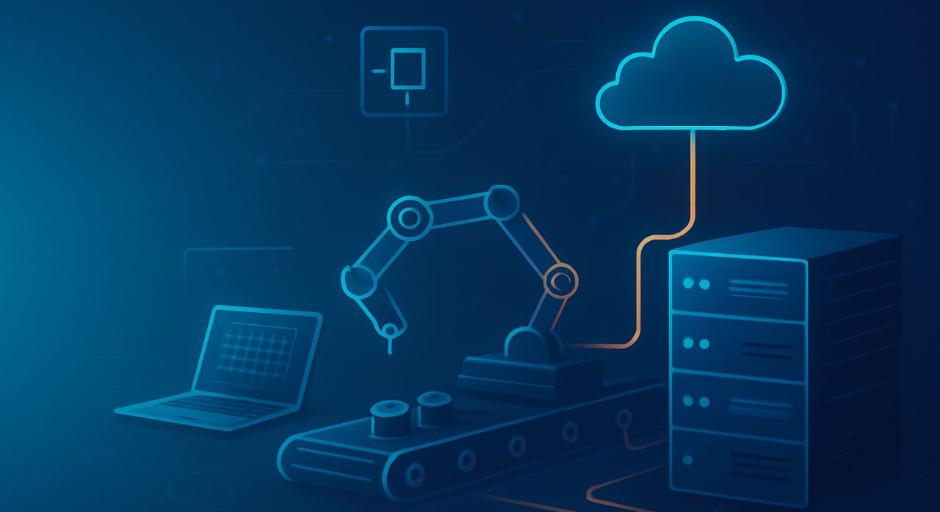
Por qué la manufactura requiere una buena infraestructura de redes
Con la adopción de tecnologías digitales en la manufactura, la infraestructura de

Transporte multimodal gana valor en la industria
En la industria manufacturera mexicana, la logística ha dejado de ser un